イントロ
樹脂成形は、プラスチック材料を加熱・加圧して成形する加工技術の総称です。用途や製品の特性に応じて、さまざまな成形方法が存在します。本コラムでは、代表的な樹脂成形の種類について解説します。
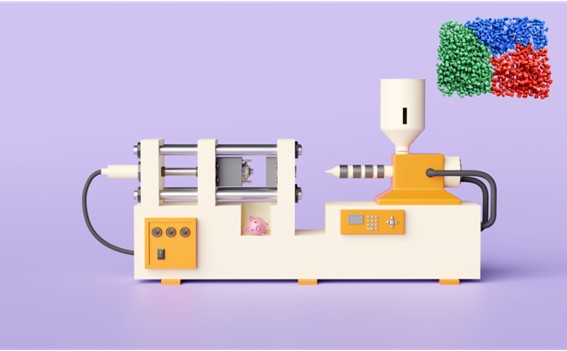
射出成形(Injection Molding)
最も一般的な成形方法で、溶かした樹脂を金型に流し込み、冷却して固める技術です。
- 特徴:高精度、大量生産向き、複雑形状の再現が可能
- 用途:自動車部品、電子機器、日用品、医療機器
押出成形(Extrusion Molding)
加熱・溶融した樹脂を金型から連続的に押し出し、一定の形状を作る方法です。
- 特徴:長尺の製品に適している、連続生産が可能
- 用途:パイプ、フィルム、シート、ワイヤー被覆
ブロー成形(Blow Molding)
加熱した樹脂チューブに空気を吹き込み、膨らませて成形する技術です。
- 特徴:中空構造の成形が可能、大量生産向き
- 用途:ペットボトル、燃料タンク、化粧品容器
真空成形(Vacuum Forming)
シート状の樹脂を加熱し、金型に押し付けながら真空吸引して成形する方法です。
- 特徴:コストが低い、大型部品に適する
- 用途:食品容器、自動車内装パネル、ディスプレイ部品
圧縮成形(Compression Molding)
樹脂を金型内で加熱・加圧しながら成形する方法です。
- 特徴:高強度な成形が可能、熱硬化性樹脂に適する
- 用途:航空宇宙部品、電気絶縁部品、工業用部品
トランスファー成形(Transfer Molding)
加熱した樹脂を圧力で金型に流し込み、成形する方法です。
- 特徴:複雑形状に対応、精密部品に適する
- 用途:電子部品、半導体封止材、医療機器
3Dプリント成形(Additive Manufacturing)
樹脂を積層して立体造形を行う新しい技術です。
- 特徴:試作向き、設計自由度が高い、少量生産向き
- 用途:試作品、カスタムパーツ、医療用インプラント
繊維強化プラスチック(Fiber Reinforced Plastic, FRP)
樹脂に炭素繊維やガラス繊維を加えて強度や剛性を向上させた高機能材料です。
- 特徴:軽量で高強度、高耐久性、設計の自由度が高い
- 用途:航空宇宙部品、自動車、スポーツ用品、インフラ構造材
まとめ
樹脂成形の種類は多岐にわたり、それぞれ異なる特徴を持ちます。製品の用途や求める特性に応じて最適な成形方法を選ぶことが重要です。技術の進化により、新たな成形方法も開発されており、今後の発展が期待されます。
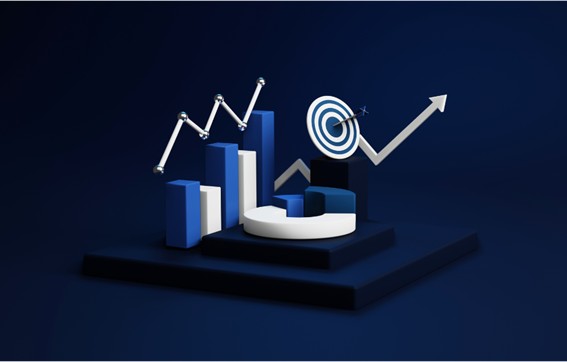
関連するお役立ちコンテンツ
ご興味のあるテーマをクリックすると関連コンテンツをご覧いただけます。
当社では、FRP・GFRP・CFRPを用いたCFRP成形加工メーカーとして多くの技術ノウハウを活用し、設計・解析から製造、二次加工・アッセンブリ、塗装、品質保証、試験までワンストップに対応しています。
UCHIDAではお客様の高度な課題にも対応できるように最先端の設備を導入しております。
DMG森精機 - VS1000/40/2050
X軸:2,050mm(ストローク) / Y軸:1,000mm / Z軸:600mm / テーブル作業面:2,250×1,000mm
芦田製作所 - AUTO CLAVE 2号機
サイズ:Ø1,150×1,000mm / 使用温度:常温〜400℃ / 設計圧力:2.0Mpa(最高使用圧力) / 真空方式:バック吸引方式 / 真空口数:5個
芦田製作所 - AUTO CLAVE 3号機
サイズ:Ø3,000×6,000mm / 使用温度:常温〜200℃ / 分布精度:±2.5℃以内 / 昇温速度:4.0℃/分(空炉) / 冷却速度:4.0℃/分(空炉) / 設計圧力:0.99Mpa(最高使用圧力) / 常用圧力:0.7Mpa以内(メーカーから指定がなければ0.3Mpa位) / 圧力精度:±0.02Mpa(0〜0.99Mpa/cm²の圧力設定に対して) / 昇圧精度:0〜0.03Mpa/min / 圧力源:圧縮空気(常用時) / 真空方式:バック吸引方式 / 真空口数:10個
オーブン
サイズ:W1,000×H1,000×D1,000mm / 温度範囲:環境温度+20〜300℃ / 昇温能力:環境温度(20〜40℃)〜300℃まで/45分以内 / 真空方式:バック吸引方式 / 真空口数:10個
オーブン
サイズ:W7,000×H3,000×D2,000mm / 温度範囲:環境温度+20〜300℃(MAX) / 昇温能力:環境温度(20〜40℃)〜300℃まで/60分以内 / 真空方式:バック吸引方式 / 真空口数:10個
NEO
X軸:4,000mm(ストローク) / Y軸:2,000mm / Z軸:1,200mm / C軸:0度〜±270度 / B軸:0度〜±110度 / テーブル作業面:4,000×2,000mm
【開発】
3Dプリンター | Markforged
塗装ブース
各種塗装・クリア仕上げ等は、専用の塗装ブースで行っています。
接着・仕上げ・コーティングルーム
型や成形物の表面処理・トリミング・穴明け・接着等の仕上げ工程は専用ブースで行っています。
東芝 - マトリックスアイEX (超音波探傷器)
Matrix-Arrey:32
AMETEK CREAFORM MetraSCAN750 Elite(3Dスキャン)
オーブン
サイズ:W450×H450×D450mm / 温度範囲:環境温度+50〜650℃ / 昇温能力:環境温度+50〜650℃/120分以内
カッティングプロッター
テーブル作業面:W1,500×L3,500mm
Krauss Maffei - エポキシ樹脂注入機
Resin 60ℓ / Hardener 25ℓ
Krauss Maffei - 630t プレス機
W1,200×L1,500×H1,700mm / Power Unit:Vacuum valve×2 / Air valve×5 / Hydraulic valve×5
DMG森精機 - NV5000B/40
X軸:1,020mm(ストローク) / Y軸:510mm / Z軸:510mm / テーブル作業面:1,320×600mm
大型クリーンルーム
JIS B 9920 清浄度クラスの上限濃度(個/立方メートル) / クラス5:100,000m³ / 室容量:256m²(16,000×16,000mm) 760m²(16,000×16,000×3,000mm) / 室内温湿度条件:温度 23℃±3℃ 湿度 65%以下 / 外気条件:夏期 温度35℃ 湿度 70%以下 / 冬期 温度-5℃ 湿度 40%以下
CAD / CAM
CATIA V5:2台 / THINK DESIGN:1台 / MASTER CAM:4台 / その他 3D/CAD:3台 / その他 2D/CAD:5台
下記動画にて製造工程を細かく紹介しております。是非ご参照ください。